July 19, 2020
Restarting Manufacturing Post-COVID
David Brashears
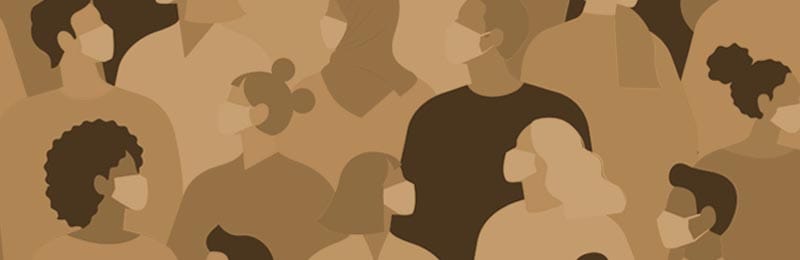
Building a reopening plan that is safe and effective
As the world begins to develop a plan for reopening many businesses in the “new normal” we’re navigating after the COVID-19 outbreak, the manufacturing industry is being forced to evaluate all aspects of their operations. With new industry and government regulations, and a higher expectation of health and safety, by employees and customers, many manufacturers have to completely rebuild their employee training and protection plans.
Unlike other sectors, like service and consulting, that could pivot to a remote working environment relatively quickly; manufacturing requires their professional staff to be working together with machinery in close quarters to produce products for their clients. This means that new protections, policies, and plans must be in place to keep staff safe and productive on the line and in every department.
The Equal Employment Opportunity Commission (EEOC) has distributed information to employers on how to safely reopen their businesses. This instruction includes several new initiatives like allowing employers to require testing to detect the virus for returning workers and taking temperatures to monitor general health of staff.
Here are a few things that manufacturers should consider as they reopen their manufacturing facilities.
Know Employee Traffic Paths
As a manufacturer, you probably already have a traffic map of how employees get to, and from, their workstations. Consider evaluating those maps to look for areas where employees congregate in larger numbers in close quarters like bathrooms, coffee stations, and break rooms. Some of these areas may need to have schedules implemented to control crowds, and some may need to be temporarily shut down to protect employees. Water fountains and other communal food and drink stations may also need to be temporarily closed to protect against multiple employee exposures.
Areas that are necessary to provide services for employees should be cleaned regularly throughout every shift to control germs and bacteria. Proper training on the preparation and use of disinfection products will ensure that areas are safer and healthier throughout facilities.
Workers should also be trained on keeping their stations clean and providing distance from other workers wherever possible. This training should include information on how to properly prepare themselves before work and how to leave workstations clean and safe for the next shift. Education is going to be critical to protect and promote employee health and safety in the Post-COVID world.
Protect Employee Privacy
As manufacturers put in place new policies and procedures that require employees to submit to testing and/or temperature monitoring, it’s going to be more important than ever that employee privacy is considered. Employee rights to personal privacy regarding their health and medical records will be an area of concern for lawmakers and government regulatory agencies.
If testing and temperature stations will be set up for employees, they need to be done in private and records need to be secured. If someone tests positive, that needs to be handled delicately and privately, while still evaluating and tracking any exposure to other employees. This will be a new system that needs to be navigated carefully to secure individual privacy and organizational protections.
Control Non-Staff Personnel Exposure
Manufacturers should control the exposure of their teams to outside personnel. Whether it is vendors, salespeople, customers, or third-party service providers, there should be a temporary restriction to interactions within the manufacturing facilities. If interaction is necessary for production efficiency, then outside personnel should be trained and comply with all protection policies in place for the company.
It can be awkward to restrict customer visits during the Post-COVID era, but in many cases digital meetings and regular teleconferences can provide an effective option that protects both organizations. Restricting evaluation of the production line can be important to help protection operations and defend against unnecessary delays and line production deficiencies that can affect profitability. Most outside teams will understand completely and recognize that the policies are in place to protect everyone. At the end of the day, it’s the manufacturing executive team to consider and develop their own policies on how to handle outside visitor exposures.
Implementing the Right Protection Equipment
The company’s Human Resource team should undergo training on government and health organization guidance on personal protection equipment (PPE) that should be used by staff. This may include facemasks, gloves, protective gowns, face shields, workstation barriers, and other equipment. Both the Centers for Disease Control and Prevention (CDC) and the World Health Organization (WHO) have extensive resources on protecting employees as they come back to work.
Whatever your company’s protective equipment plan becomes, it will be critical that you have a reliable supply chain and good stocks of all equipment to provide for your team. It will also be important to ensure that all the new PPE complies with the Occupational Safety and Health Administration (OSHA) regulations to ensure against injuries or issues caused by the equipment on the production lines.
Evaluate Supply Chain Exposure
It’s also going to be more important than ever to control all materials coming into the facilities. Whether you’re using sourced components or reusable packing materials, your company should ensure that everything coming into the facility is following good health and safety guidance to protect your workforce.
All materials should be cleaned and sanitized if necessary, and all those handling this material should be properly protected to ensure a healthy work environment. It can be incredibly detrimental to have sourced components and materials introduce virus and germs to your team, causing lost work and production impacts.
Your procurement team should also have meetings with all supply chain partners to understand how they are providing sound and safe production of those components they are supplying to your facilities. Vendors should be able to provide evidence of how their team operates in a healthy environment and how packaging and shipping is handled to limit any potential exposures.
It is an exciting time to see manufacturing facilities begin to reopen and begin producing all the products we need to reinvigorate our economy. Doing so in a healthy manner will ensure that our economy can bounce back quickly, and employees can have confidence to do their work safely and efficiently for your company.
If you are a manufacturer in need of help and guidance in developing training and materials to educate your staff on how your business will operate in a Post-COVID marketplace, contact Creative Energy. Our team has nearly 30 years of experiencing helping manufacturers create tools to work effectively and grow in a healthy way. We’re ready to help you get back to work and succeed.
Get insights delivered straight to your inbox.